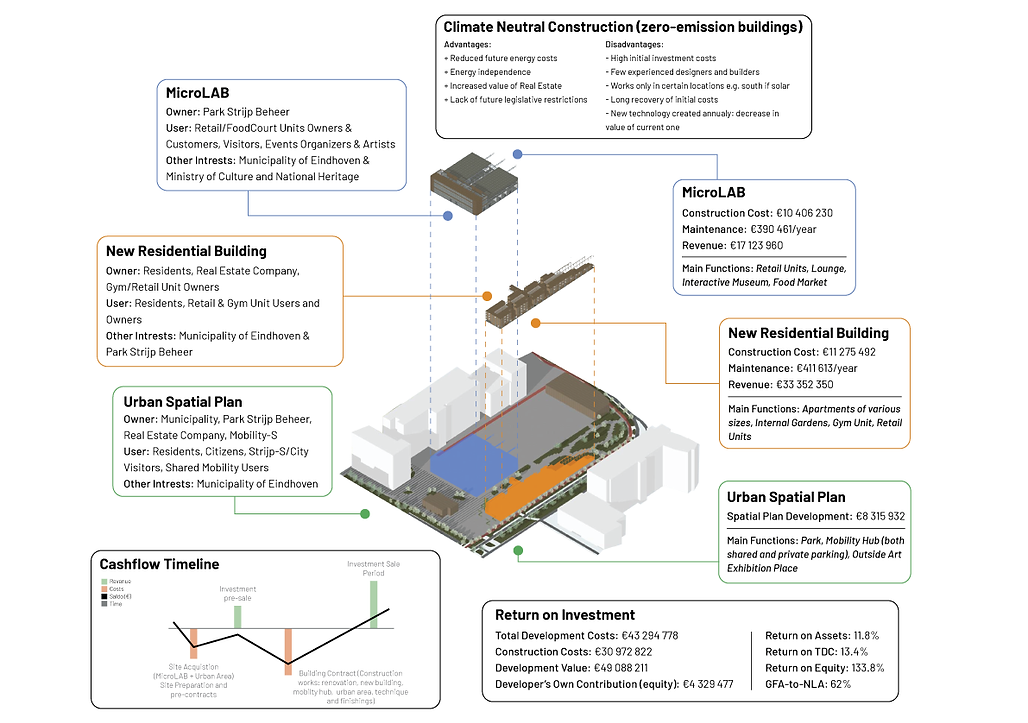
FINANCIAL FEASABILITY
RECRE8/2 being the 4th phase of the Strijp-S transformation brings moderate, yet innovative and vibrant interventions. The estate will be hosting multiple functions and serve not only its end-users, but also the entire city of Eindhoven. The mixed-use development tackles urban densification in Eindhoven while creating a human scale environment for starters. A demountable residential building embodies modularity with human scale architecture. Centered around a set of flexible exhibition and workshop spaces, the mixed-use development provides both residents and visitors with local retail units, a vibrant food market, and a gym facility. This is all immersed into a green and lively urban space with a shopping street, a public square, exhibitions in a park and a shared mobility hub for easy transportation. After a thorough investigation and cost estimation, one can proudly say that this real estate development is not only financially feasible, but also an extremely attractive investment. Construction brings around 12% of return on assets and around 134% return on equity.
SUSTAINABILITY
RECRE8/2 aims to reach the goal of energy neutrality in 2050. Renewable energy produced by solar panels goes towards the operation of the various functions of the buildings and the embodied energy of construction materials. For both buildings an optimal amount of solar panels is found ensuring compensation of embodied energy using the solar energy surplus.


PHOTOVOLTAIC GENERATION
Having a great return on investment in the long run, the newest mono-crystalline solar panels are used for all buildings. In order to get the most out of the solar panels, optimal placement is determined by performing sun hour analysis. In the extension of the Microlab West Wing photovoltaic glass is applied, which functions as shading in the summer months.
MATERIALIZATION
With a focus on sustainability, the main building material is timber due to its low embodied energy. However, not limited to this, also its ease-of-use in construction is a large benefit. The columns are made of glulam and the floor slabs and shear walls of Holz100 elements. Holz100 is a timber slab material that uses the principle of dowels. It performs structurally similar to CLT, but it has no chemicals as the glued connection is replaced by dowel action. The members can be prefabricated and transport to site, then due to the modular nature of the design the building can be erected relatively fast compared to for example pouring concrete. For the ground floor, it is chosen to use concrete, this is to ensure a durable and long-term base of the building that can always be reused for later projects or transformations. The ability to transform the building is a requirement for the structural vision, this is achieved by using connections that can always be disassembled in the future. For example, the use of screws and bolts instead of glued connections or cast-in-place layers. This ensures that the building can always be transformed or disassembled and reused for a new purpose. Allowing for a more sustainable building design and longer life-span of the materials.
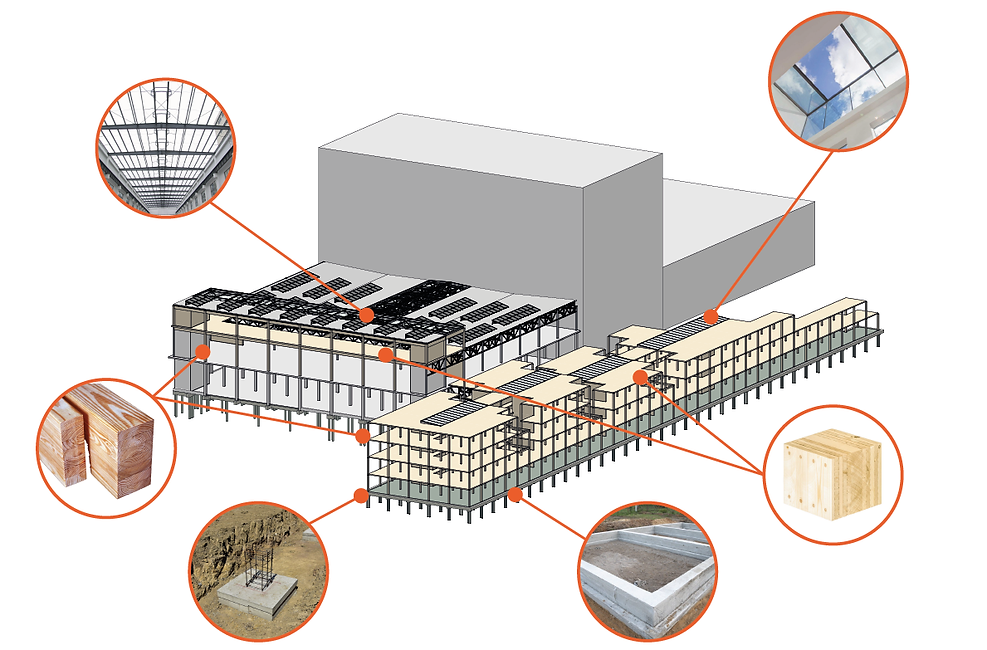

TRANSPORT
In order to minimize transport and optimize the construction process it is desired to transport all elements with regular transport. Strijp-S is deeply nestled within the city and surrounded by crossings of maximum 4m height. Therefore, the standardized elements must be dimensioned such that they fit on a regular trailer in order to meet the vision. To realize this a double drop trailer is used where the largest elements are the 3.6m high façade panels. This ensures everything can be delivered with ease to the site. On-site a crane with a 60m radius can reach almost every part of the project. The area that is not covered by the crane can be accessed by a telescopic handler. This setup ensures the most efficient transfer of materials with the least amount of machines.

CONSTRUCTION SITE